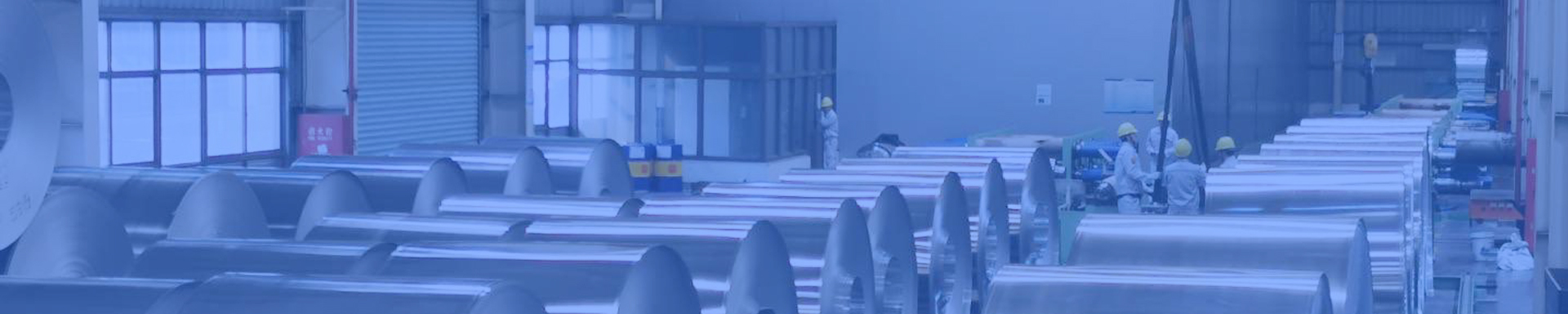
Холоднопрокатный стан Машина Боковой Рабочей Роликовой Подшипниковой Блок
Основные функции и требования к условиям работы подшипникового узла рабочего валка на рабочей стороне стана холодной прокатки
Основные функции
Высокая точность позиционирования: убедитесь, что радиальное биение рабочего валка составляет ≤ 0,01 мм (с допуском по толщине ± 1 мкм для прокатки тонкой полосовой стали)
Быстрая смена рулонов: встроенный гидравлический механизм блокировки (время смены рулонов ≤ 10 минут)
Подавление вибрации: контроль высокочастотных вибраций в диапазоне 20–500 Гц (амплитуда ≤ 0,5 мкм)
Совместимые модели
Шестивалковый прокатный стан УК-МЕЛЬНИЦА: толщина прокатки нержавеющей стали/кремнистой стали 0,1-2,0 мм
Двадцативалковый прокатный стан Сендзимира: производство сверхтонкой полосы (0,02-0,2 мм)
- GW Precision
- Лоян, Китай
- Договорное положение
- Годовая производительность 1000 шт.
- Информация
Холоднопрокатный стан Машина Боковой Рабочей Роликовой Подшипниковой Блок
Спецификация материалов и термической обработки для рабочего посадочного места роликового подшипника
Основной материал
Марка: ковкий чугун QT600-3 (RU-GJS-600-3)
Оптимизация ингредиентов:
|Элемент | C 3,6-3,8 | Си 2,2-2,5 | Мн ≤ 0,3 | Мг 0,03-0,05|
Эксплуатационные характеристики:
Характеристики демпфирования (степень затухания вибрации ≥ 35%)
Лучшее соотношение прочности и веса, чем у литой стали (плотность 7,1 г/см³)
Материалы ключевых компонентов рабочего седла роликового подшипника
Компонент материал термическая обработка обработка поверхности
Корпус рабочего роликового подшипника QT600-3 изотермическая закалка дробеструйное упрочнение (0,3 мА)
Износостойкая футеровка GCr15SiMn глубокая холодная обработка с твердым хромированием (20 мкм)
Уплотнительный компонент ПТФЭ+316L - лазерная микротекстура
ГВ прецизионный процесс термообработки гнезда роликового подшипника
Изотермическая закалка:
900 ℃× 2ч → Закалка в соляной ванне (300 ℃× 1ч) → Охлаждение на воздухе
Обработка для обеспечения стабильности размеров:
180 ℃ × 24 ч старения (изменение размера ≤ 0,005%)
1. Вертикальный обрабатывающий центр:В соответствии с формой вида глубина фрезерования составляет 5 мм, чтобы найти положительный ремень (с каждой стороны есть место для 1,5-2 мм); очистите и удалите заусенцы с острой кромки для проверки (первая часть для проверки).
2、 Горизонтально-расточной станок:Установлено, что для каждой поверхности обычного ремня оставлен запас в 1,5–2 мм, а запас канавки на виде составляет 1,5–2 мм; запас отверстия в отверстии составляет 3–4 мм; длина каждого отверстия составляет 2–3 мм; а чистый край используется для удаления острого края заусенца для осмотра. (первый образец для осмотра)
3. Вертикальный обрабатывающий центр:Окончательная фрезеровка (поверхность без допуска) выполняется в соответствии с требованиями, длина фрезерования должна быть равна глубине правильного края 5 мм; расточка должна соответствовать требованиям, остаточный размер каждой стороны должен составлять 1 ≤ 1,5 мм; длина каждого отверстия должна соответствовать требованиям, а точка должна совпадать с двумя концами центрального отверстия; необходимо обеспечить допуск по размеру, форме и положению.
4. Горизонтальный обрабатывающий центр:Верхняя оснастка, длина выравнивания и кромка выравнивания основаны на среднем отверстии, и все стороны соответствуют требованиям; И направьте центральное отверстие каждого отверстия на торцевую поверхность, чтобы обеспечить допуск каждого размера и формы; Глубокая обработка отверстия в соответствии с требованиями; Обеспечьте допуск размера;
5. Вертикальный обрабатывающий центр: Исходное отверстие в качестве ориентира, чистовое расточное отверстие, в соответствии с требованиями; Обработка отверстия в соответствии с разницей, а затем использование прокатного ножа для прокатки поверхности отверстия; Чтобы гарантировать допуск каждого отверстия, необходимо провести испытание, чтобы сохранить припуск в 1 мм перед обработкой по размеру. Очистите и удалите острые края заусенцев для проверки.
6、 Слесарные работы:Каждое нижнее отверстие резьбы позиционирует отверстие в соответствии с требованиями.
7. Слесарные работы: Другие отверстия для масла и резьбовые отверстия; Очистите и удалите острые края заусенцев для проверки. (первая деталь для проверки)
8. Окончательная проверка: удалить острые края заусенцев путем очистки и отправить на проверку, а также выдать контрольный лист.
Точность механической обработки рабочего гнезда роликового подшипника
Критические допуски размеров
Метод испытания на уровень допуска обрабатываемых деталей
Отверстие подшипника (Φ 200-400 мм) электронный калибр-пробка IT4 + тестер круглости
Плоскостность монтажной поверхности гидроцилиндра 0,01 мм оптический плоский кристалл
Отверстие для позиционирования штифта H6 координатно-измерительная машина
Позиционный допуск
Цилиндричность отверстия подшипника ≤ 0,003 мм
Вертикальность каждой монтажной поверхности ≤ 0,005 мм/100 мм
Совершенная система управления качеством, эффективная гарантия послепродажного обслуживания, благодаря чему рабочие роликовые подшипниковые опоры компании завоевали хорошую репутацию.
Система смазки и герметизации гнезда подшипника рабочего ролика
Система масляно-воздушной смазки
Масло: синтетический эфир ИСО ВГ 68 (содержащий присадку МоС₂)
Параметры:
Объем масла 0,05 мл/раз
Давление воздуха 0,4-0,6МПа
Частота 2-5 Гц (автоматически регулируется в зависимости от скорости прокатки)
Многоступенчатая герметизация
Первый шаг: Магнитно-жидкостное уплотнение (сопротивление давлению 0,15 МПа)
Второй шаг: механическое уплотнение из карбида кремния
Третий шаг: Газовое уплотнение лабиринтного типа (защита N2)